Expertise
Acmena's unique combination of expertise and experience enables us to deliver fully integrated, end-to-end solutions for our clients’ projects.
We specialise in developing pragmatic, scaleable strategies for complex, safety-critical applications in highly regulated industries.
Whether you require expertise in a single area, or a multi-discipline team, our consultants will work with you to develop solutions that fit the specific needs of your project and ensure it is delivered in less time and with greater certainty.
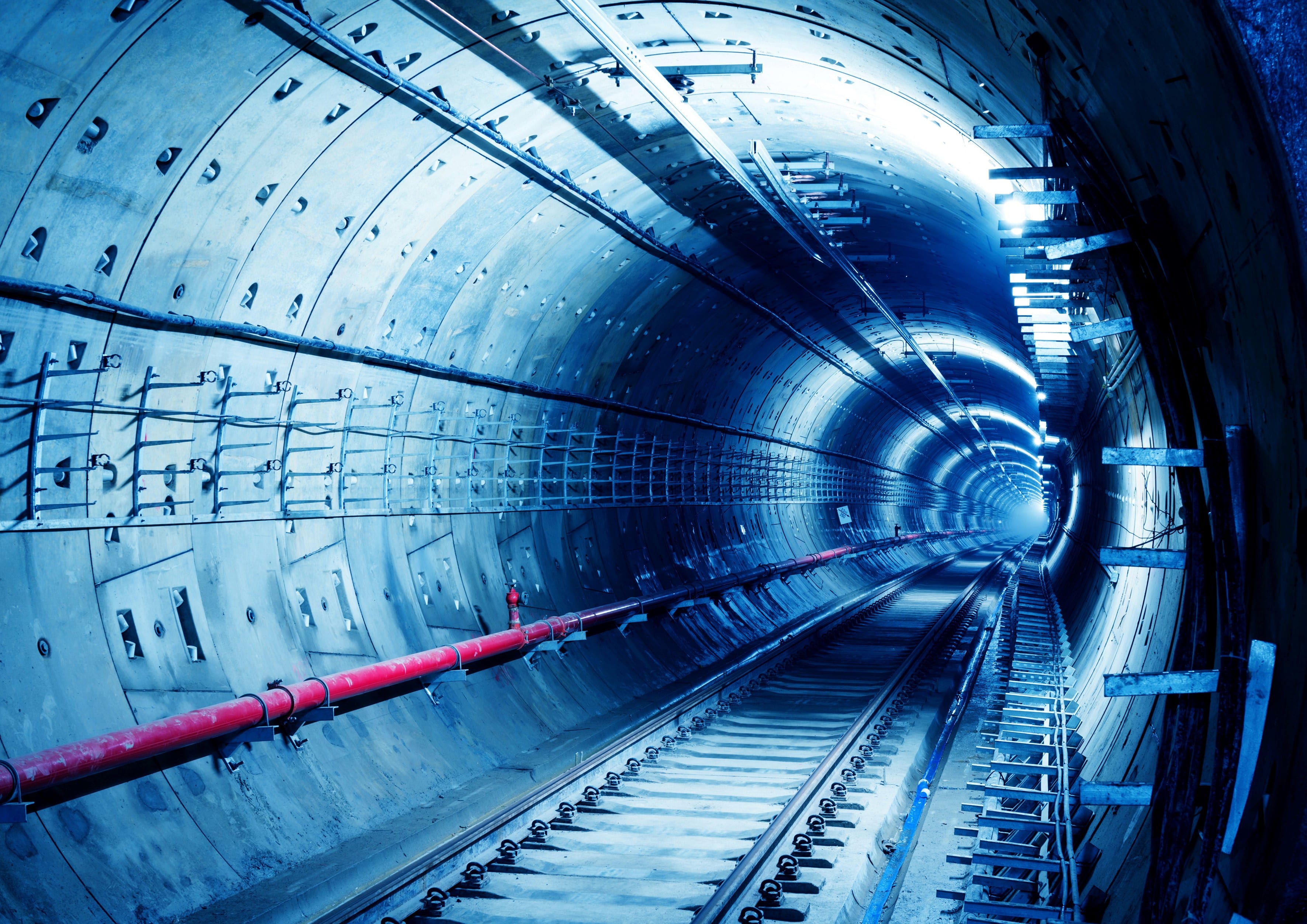
Our expertise
-
Systems Engineering & Integration
As project complexity rises with size and sophistication, so too does the risk of unforeseen complications, budget overruns and failure to meet requirements or objectives.
Learn more -
Human Factors
Developing better, safer systems requires a deep understanding of peoples’ needs, capabilities and behaviours.
Learn more -
System & Safety Assurance
When developing safety-critical systems, you need to have justified confidence that they will perform as intended and remain safe throughout their projected lifespan, which is why Acmena offers a range of systems and safety assurance services to support the complete lifecycle of your project's assets.
Learn more -
Risk Management
When systems designed for safety-critical applications fail, the consequences can often be extensive and severe.
Learn more -
Engineering Management
As project complexity grows, so too does the need for a holistic, interdisciplinary approach to engineering management.
Learn more -
Advanced Technologies & Software Assurance
Acmena specialises in the development of advanced technologies and software-intensive systems.
Learn more